|
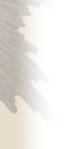 |
Mike
Estelmann
Perhaps
no other military decoration is as significant as the Iron
Cross. At a minimum, this statement is true for the
foundation year series of 1813 and, at a respectful
distance, the 1870 series. The historical dimension, the
engaging symmetrical aesthetic, and the appealing
juxtaposition of two metals which could not be more
different from one another, only begin to explain why
contemporary examples of this patriotic decoration are in
such high demand. As this demand is now so high, and there
are an insufficient number of originals, there has followed
what must: modern copies. These copies may be revealed
through the use of relevant literature, photo documentation,
and comparative analysis with known originals. To begin
with, of course, we have the words of the Old Master of
Prussian Militaria-writing. Louis Schneider, the Privy Court
Councilor and Reader of his Majesty the King, notes in his
1872 work, The Book of the Iron Cross, that King Wilhelm I
re-instituted the Iron Cross with an order dated 19 July
1870, the very day of his beloved mother Queen Luise's
death. He continues: On 30 July, the day before the
departure of the king to join his army, the president of the
General Order Commission, Adjutant General v. Bonin,
presented an 1870 Iron Cross, finished that same day, to the
king. Wilhelm himself wrote on the accompanying letter from
General v. Bonin: "Approved." Thus the order was
given to the director of the Iron Foundry, Bergrath Schmidt,
to begin casting the crosses according to the model. On 11
August, Director Schmidt announced to the jewelers
authorized to make the silver frames that the Iron Cross
cores could be picked up. Furthermore, Schneider recounts
his manufacturing figures in detail, and states in summary
that, by command of His Majesty the King, a total of 44,489
crosses had been delivered as of July, 1871 from the General
Order Commission to the Military Cabinet. The foundry to
which Schneider refers is the Royal Iron Foundry in Berlin,
founded in 1804 and located in front of the Oranienburger
Gate. In addition to the Royal Iron Foundry in Gleiwitz, the
Royal Iron Foundry in Berlin manufactured cores for Iron
Crosses during the Napoleonic Wars of Liberation. For our
purposes here, we must investigate the manufacturing
techniques and connections of the time. The Berlin Foundry
had a high technical "know-how," and when
undertaking to manufacture 1870 cores its artisans could
look back with pride on a long and successful company
history. From their workshops, for example, were built, in
1816, the first two gear-wheel steam locomotives in
continental Europe, the Kreuzberg Monument for the Wars of
Liberation in Berlin, and the Berlin castle bridge, which to
this day testifies to the Foundry's efficacy from its spot
on Berlin's Invalidenstraße. But the Foundry did not
undertake only large-scale projects. Its experience with
decorative artwork and delicate jewelry seemed to make it
the perfect choice to manufacture the cores for the Iron
Cross. Let us investigate the workshops and production
techniques to learn more about our subject. After the
confirmation of the new core design, the first step was to
make a wax model from which a master mold would be made with
a soft metal like tin or silver. Then sand -- sifted several
times through a linen cloth and kneaded with clay -- was
mixed with water and tapped by a hammer into the mold until
it was tightly compacted. After smoothing, the workpieces
were pressed in and then the second, already prepared side
of the mold could be attached and assembled under high
pressure. After the separation of the two halves -- which
could be accomplished without difficulty as the contact
faces had been powdered with coal dust before -- the master
pieces could be removed leaving the remaining imprints
connected by fine channels. This is how a so-called casting
tree was produced. After the finished casting molds dried,
the actual casting began. Experienced workers poured the
molten iron from a melting pot into the provided openings of
the mold, where the iron flowed evenly into the hollows.
Through previously-applied outlets, the suppressed air
escaped. This technique allowed the production of high
quantities in the shortest time (Fig. 1).
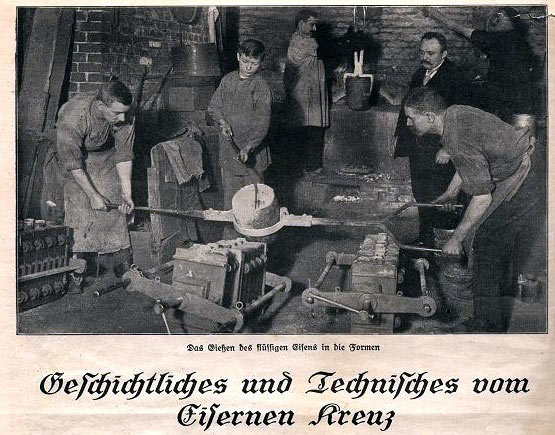
Fig.
1: The illustrated magazine "Stein der Weisen,"
published at the beginning of World War I, shows the
tradional process for manufacturing the Iron Cross.
Initially, each core was cast. However, the astounsing
number of Iron Crosses awarded -- over 5 miliion in World
War I -- soon made other techniques necessary.
Why guess?! Get the expert's opinion at

|
After the
solidification process of the iron, the molds were separated
and the cores removed by means of a slight knock, or tap, on
the side of the mold. With a polishing stone the cores were
finished by hand and given the desired look of fine jewelry.
Then followed the process of annealing, or removing inner
stress through a process of heating and gradually cooling
again. Next, the cores were again evenly heated, and a dark
varnish made from linseed oil, resin, and galena black
carbon was applied. A final rapid heating caused the oil to
evaporate, leaving the iron cores with that durable
matte-black finish typical of the Iron Cross. This finishing
process is also known as "false blackening," and
has nothing in common with real blackening in which there is
a chemical reaction of the base material itself and a kind
of patina forms. In the case of "false
blackening," a thin, highly adhesive coating adheres to
the core, creating the so-called "blackening."
From the evidence so far observed, we may now draw our first
conclusions. The majority of Iron Crosses awarded during the
campaigns of 1870-1871 must have identical cores, since they
were all manufactured at the Royal Iron Foundry in Berlin.
Minor differences are due to the aforementioned
manufacturing and finishing method. Only the frames should
exhibit marked differences, since they were made by several
different jewelers. But here again we must reference
Schneider, who states in his book that as late as March
1872, several thousand Noncombatant First and Second class
crosses remained to be awarded. He does not mention where
these later-awarded examples originated. A further order
from the Royal Iron Foundry is probable, and Schneider may
have made no mention of it on the assumption that it was
understood. With the following photo documentation we may
try to further understand our subject. It should be noted
that an assignation of a manufacturer to the 1870 EK2 can
only come from comparison with marked First class
crosses(Fig. 2).
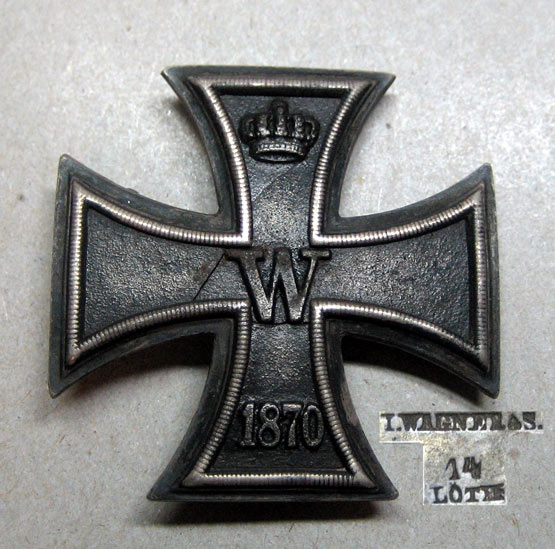
Fig.
2: Iron Cross First Class marked for Johann Wagner &
Sohn, Berlin
Exactly
this core type, with its distinctive date and crown design
(Fig. 3), is to be found on most Second class Iron Crosses,
and it may be assumed that it is this type described by
Scheider and made in the Berlin Foundry.
Fig.
3: Iron Cross Second Class. The core design is identical to
the FIrst Class example illustrated above.
Further
clues are to be found in the available literature on the
history of military decorations. Jorg Nimmergut, in Volume 2
of his book, German Medals and Decorations to 1945, shows an
engraved EK1 from ex-Kaiser Wilhelm II's Huis Doorn, with a
core identical to those previously described. This cross is
his father Crown Prince Friedrich Wilhelm's personal
example, awarded on 20 August 1870. Also, former Chancellor
Bismarck's EK1, shown in the recently-published book of his
awards, exhibits an identical core. Furthermore, this core
type may be seen in contemporary photographs (Fig. 4-6).
Fig.
4: The War Minister to-be, Karl von Einem gen. von Rothmaler.
Fig.
5: Lieutenant General Bernhard of Austria
Fig.
6: Details of Iron Crosses worn by unknown recipients
This core
type shall now be designated "Type A." All
examined Iron Crosses with this Type A core have the
following characteristics: - The cores are cast. - The size
varies by tenths of a millimeter, and only very rarely
exceeds 42mm. - The weight can be between 15.6 and 17.5
grams. - The jump ring is affixed very near the top and is
usually open (unsoldered) on one side. Never has a maker
mark or a silver-content mark been seen on the ribbon ring.
(Fig. 7)
Fig.
7: Jump rings open (unsoldered) on one side.
The cores
are not painted, but blackened as described above (Fig.
8)
Fig.
8: Reverse of a "blackened" Type A core.
After
core Type A, we must now consider a second type with
different characteristics. Again, assignment of a maker has
been accomplished by comparison to marked First class
crosses. This core shall be called "Type B." The
illustrations show a First class Iron Cross made by Godet,
Berlin, and an example of a Second class with the same core
(Fig. 9-10).
Fig.
9: EK1 marked for Godet. Characteristics of this core
include the slim numbers in the date, the slightly leaning
"8", and the tall, narrow "0".
Fig.
10: EK2 with leaning "8" and high, slender
"0".
Supporting
contemporary evidence is again provided by "The Great
Nimmergut." There is a cross of this type in the
possession of Kaiser and King Wilhelm I and shown in The
Prussian Cultural Heritage Foundation. This core type is
also easily discernable in contemporary photographs (Fig
11).
Fig.
11: The Type B core can clearly be seen on this unknown
veteran's bar. Photo: Aron Willers, Friedrichshafen.
Type B
cores have the following characteristics: - The cores are
cast. - The size varies by tenths of a millimeter, and
occasionally exceeds 42mm. - The determination of weights is
somewhat distorted by the fact that a number of examined
crosses exhibited repairs. At the lower end of the scale is
16 grams. However, it is important to note that no example
weighed over 17.6 grams. - The cores are not painted, but
blackened (Fig. 12).
Fig.
12: Reverse of a "blackened" Type B core.
- The
jump ring is also attached near the top, is usually open on
one side. Again, no manufacturers or silver-content marks
were seen. The evidence above permits the conclusion that
there were two contemporary core types, designated here as
Type A and Type B. The essential characteristics -- casting,
blackening instead of painting, high and almost identical
jump ring, weight and size tolerance -- are very similar.
Only in the design of the core details may differences be
found. The continuing pursuit of our quarry leads us to the
year 1874. Although not previously noted in the study of
this subject, it is nevertheless true that the Royal
Prussian Iron Foundry in Berlin was closed in this year.
Kaiser Wilhelm I issued the order for closing the Foundry on
31 March 1873, and the last cast was made on 5 January 1874.
The inventory of the foundry was sold at auction to other
state enterprises and institutions. Not only does this
development represent the end of a historically and
culturally valuable era of art and Iron work in Berlin, it
also raises the interesting question of who, after the
Foundry's closing, was able to manufacture cores to meet the
demand for replacement Iron Crosses. Inseparable from this
question is the existence of core Type B. As we have seen,
Type B cores were used by Godet of Berlin. Moreover, as of
this writing, they have been seen exclusively in Godet
crosses. There exist no other crosses clearly attributable
to a different manufacturer with this core type. This stands
in contrast to Type A cores, which are clearly to be found
in crosses assembled by jewelers other than Wagner of
Berlin. Let us remind ourselves of Schneider's observations:
"Director Schmidt announced to the jewelers authorized
to make the silver frames that the Iron Cross cores could be
picked up." If you infer from this statement that
several jewelers arrived to pick up the finished cores from
the Berlin Foundry, it becomes clear why Type A cores are to
be found enclosed within frames manufactured by multiple
companies, and why there are EK1s marked by various
jewelers, including Godet, with Type A cores (Fig. 13).
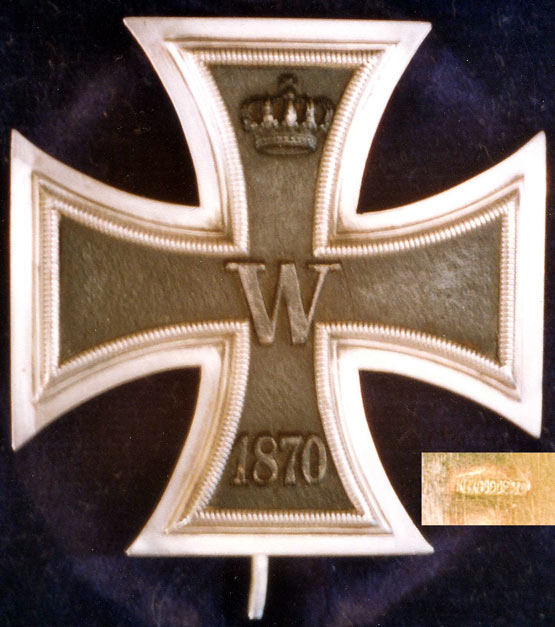
Fig.
13: EK1 with Type A core, but marked for Godet. Photo:
Markus Bodeux, Herne.
But Type
B cores are known only in Godet frames. We may now conclude
that Godet either made, or had made, Type B cores. An
interesting corollary may be found in secondary literature.
In Friedhelm Heyde's standard Iron Cross reference book on
the collection of Max Aurich, published in 1980, the author
writes about recipients of the 1813 Iron Cross who received
their awards after the end of the Napoleonic Wars: Whether
the casting of the iron cores was accomplished in the Kgl.
Preuß. Eisengießerei Berlin (Gleiwitz) or at the iron
foundry of the respected manufacturer of religious jewelry,
Godet, has not been conclusively established. This means, of
course, that Godet did have the means at their disposal to
make the iron cores themselves. Also, as anyone interested
in the history of military decorations is aware, there was a
strong urge for companies to keep everything in-house --
both manufacturing and design. Examples of Godet's own urge
to individuate their designs are to be found in their unique
swords, the completely different design of their First class
Prussian Red Cross medal, and their stylistically divergent
Prussian Stars. Core Type B, with its completely different
design, fits in this list rather nicely. Such a venture
would have been economically beneficial as well, for not
only were duplicate pieces needed, but replacement crosses
would have been required by those who either lost their
originals, or whose originals suffered from the common
breakage of the jump ring. The latter problem was already
known from the first crosses. Why the problem was not fixed
for later crosses is not known. Perhaps, as has been
suggested, the research and retooling required was not
cost-effective, an example of questionable craftsman logic.
(Fig. 14-15).
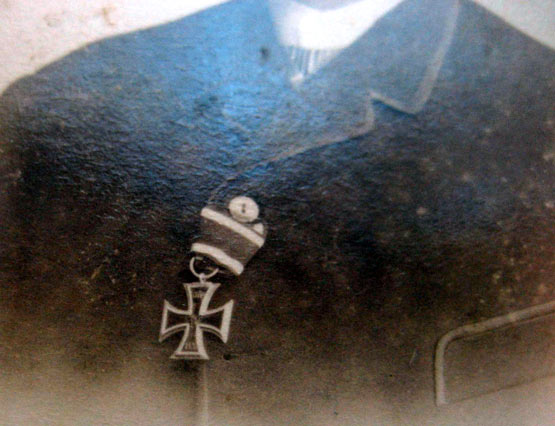
Fig.
14: Clearly visible is the repair to this EK2.
Fig.
15: A period repair to the jump ring.
At this
point we may make a preliminary summary of our findings:
Core Type A and Type B are both contemporary to the award
period. Type A cores, made at the Berlin Foundry, were
distributed to several jewelers, but predominantly Wagner of
Berlin, for use in award and private-purchase Iron Crosses.
Type B cores, probably manufactured in-house by Godet, were
used in duplicates and replacement crosses. In this context,
it is worth mentioning that crosses with core Type B are
found far more frequently mounted on medalbars (großen
Ordensspangen) than are Type A crosses, a fact which tends
to support the theory that they were manufactured as
secondary pieces. After this excursion into manufacturing,
production techniques and historical context, we must now
describe yet another type of cross. It is a type which can
not be found in any known period groupings, nor can it's
provenance be established by any other supporting
documentation or evidence. Moreover, it is only in recent
years that this type has been seen in the marketplace. This
statement is further confirmed by the fact that no examples
of this type may be seen in Friedhelm Heyde's book on the
Aurich collection. Neither can such a type be identified in
Harald Geißler's 1995 Iron Cross book. In Jorg Nimmergut's
previously cited book, published in 1997, there are only
images of core Type A and core Type B crosses. Only newer
publications, such as American author Steven Thomas
Previtera's The Iron Time, published in 2007, show this type
of cross. (Fig. 16-21)
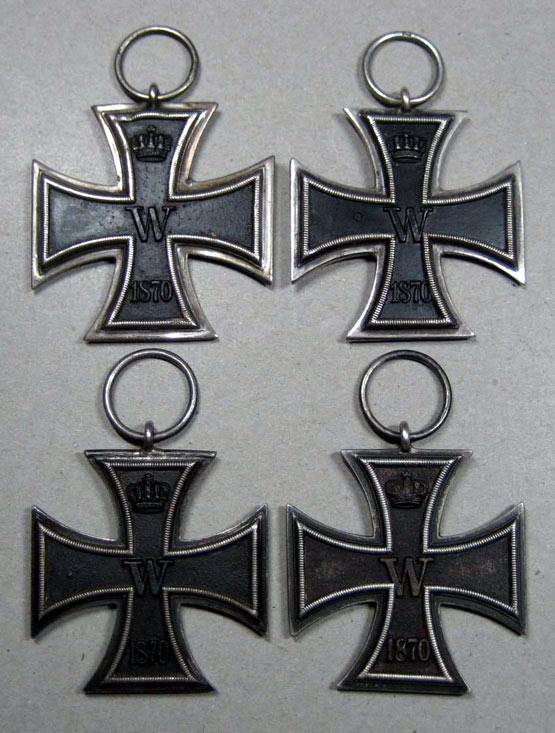
Fig.
16: The two crosses in the top row are clearly larger than
the Type A and Type B core crosses in the bottom row.
The
characteristics of this type of cross are listed below: -
The cores are not cast, but stamped. - The crosses are
larger and vary in size from 42 to 44 millimeters. - They
are much heavier and generally weigh over 19 grams. - The
ninth bead in the headband of the obverse crown is generally
somewhat larger than the others, slightly offset to the
bottom, and quite noticeably protuberant.
Fig.
17: Obverse crown with protuberant ninth bead. Also note
maker's mark "Z" or "N" on the ribbon
ring.
- The
crossing lines on the "8" on the core date are not
on the same level as in Type A cores, but rather one crosses
noticeably over the other. This is known as an
"over-and-under 8."
Fig.
18: The "over-and-under 8.".
- On the
reverse side date, there are deep flaws in the lower
portions of the "8" and the middle "1".
Fig.
19: The date flaws on the reverse.
- The
jump ring is heavily soldered and sits lower on the frame;
the ribbon ring almost always exhibits a marker's mark.
Fig.
20: Maker's mark "L" on the ribbon ring, and the
characteristic ninth bead in the crown's headband.
- The
cores are all painted and not blackened.
Fig.
21: Clearly visible is the core's paint, and the oversize
ninth bead.
That
these crosses are not originals should be evident by
Schneider's remarks as well as by the total absence of
illustrations and discussions in earlier literature.
However, the argument that these are original pieces, or
contemporary duplicates, is heard time and again. There is
no doubt that there was a demand for replacement crosses.
Indeed, the need to address breakage problems and the 25th
anniversary of the Iron Cross's re-institution would have
raised this demand. Thus it is not proper to dismiss
outright any cross that does not have either a Type A or a
Type B core, as the market for second pieces surely gave
rise to different variants. Figures 22 and 23 show an
example that was certainly a contemporary secondary piece.
The painted core of this example resembles a Type A, but
clearly deviates in some details.
Fig.
22: Obverse of a replacement cross.
Fig.
23: Reverse of a replacement cross.
However,
in light of known manufacturing techniques, the cross is
question shows itself to be highly suspicious. Size and
weight of these pieces correspond to the average values of
World War I Iron Crosses and are significantly over accepted
tolerances for core Type A and core Type B 1870 Iron
Crosses. The jump ring attachment is identical to 1914 EK2s,
and the stamped cores are painted, again as with 1914 EKs.
But the list of suspicions is not yet exhausted. Maker's
marks are found on the ribbon rings. These markings are
easily identifiable as World War I codings. At this point,
the weight of the evidence clearly establishes that these
crosses are modern counterfeits, or fakes, made from newly
minted cores and genuine World War I Iron Cross frames. This
fake is called "The Ninth Bead Fake," and is known
with the following maker's marks on the ring: L, WS, Wilm, N
or Z, KO, CD 800, MFH, G, K.A.G., L.W., IVI, R-W -- next to
KO, K.A.G. and CD, the most common maker's marks from
1914-series Iron Crosses. The instinctive notion that these
may be legitimate duplicates made for veterans during World
War I may be rejected on two counts: first, the logic of
biology dictates that demand would have been very low for
1870 Iron Crosses after 1914, and second, no contemporary
manufacturer could have made the quantity of these Ninth
Bead Fakes on the market today and still met their
obligations to manufacture 1914-series crosses; they
dominate today's market in disconcerting numbers. It would
be a mistake, however, to imagine that there was no
production of 1870 Iron Crosses after 1918. There was indeed
a small, but verifiable, production of such awards. The
manufacturing quality of Ninth Bead Fakes, however, does not
compare favorably with World War I-made pieces. This
discrepancy, combined with their increased numbers in recent
years, does not permit any classification other than
contemporary fake. This verdict is further supported by the
extremely unprofessional way the frame halves have been
rejoined after the cores were exchanged. Original pieces
always exhibit a finely soldered seam -- testimony to the
high skill of contemporary silversmiths. Mastery of this
skill may be confidently assigned to World War I-era
craftsmen also; thus the Ninth Bead Fakes can not have been
made during either period. Moreover there is not even the
slightest possibility that the frames were opened and
rejoined during World War I, as anyone with a need would
have had access to freshly made original frames (Fig. 24).
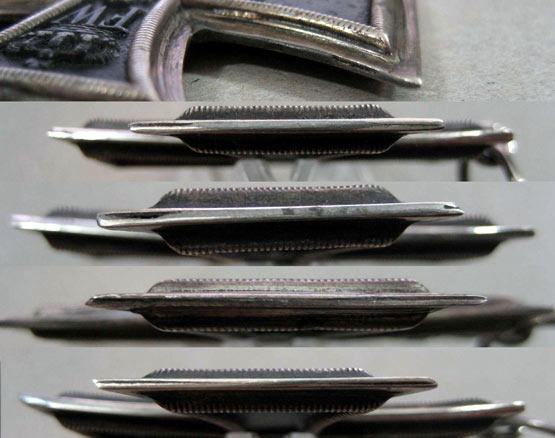
Fig.
24: A selection of poorly resoldered frames on examples of
the "Ninth Bead Fake."
This last
unambiguous evidence that the Ninth Bead examples are fakes
-- the unprofessional resoldering of the frames -- may
signal the final disappearance of these fakes from the hobby
and the market. But the final farewell may not have yet been
heard, unfortunately, for it must be mentioned that,
although rare, First Class examples of this fake have been
seen.
Special
Thanks to: Trevor, Markus Bodeux, Herne, Michael Fischer, Ladenburg
and an anonymous specialist.
Literatur:
Arndt, L. / Müller-Wusterwitz. N., Die Orden und
Ehrenzeichen des Reichskanzlers Fürst Otto von Bismarck,
Offenbach, 2008. Geißler, H., Das Eiserne Kreuz,
Norderstedt, 1995. Hessenthal, W. v. / Schreiber, G., Die
tragbaren Ehrenzeichen des Deutschen Reiches, Berlin 1940.
Heyde, Friedhelm, Monographien zur Numismatik und
Ordenskunde, Preußen-Sammlung Max Aurich, Teil C, Das
Eiserne Kreuz, Osnabrück, 1980. Meyers großes
Konversationslexikon, sechste Auflage, Leipzig und Wien,
Bibliographisches Institut, 1905. Nimmergut, J., Deutsche
Orden und Ehrenzeichen, Band 2, München, 1997. Previtera,
S.T., The Iron Time, Richmond, 2007. Schneider, L., Das Buch
vom Eisernen Kreuze, Berlin 1872 Schreiter, Ch. / Pyritz,
A., Berliner Eisen, Hannover, 2007
©
Andreas M. Schulze Ising VII/2009 |
| |